So now that we know a little about wire, what are we connecting?
Much like wire and wire gage, the type of connector is often an outcome of what needs to be connected to what. The “trick” here is to know what is commonly used in a situation similar to yours, and purchase that. For example, the signals sent from an MP3 player to headphones are at a similar level to say, a temperature sensor’s signal. So, if you need to connect the three terminals of a temperature sensor (power, ground and signal), using a standard stereo headphone jack and mating connector would be a good place to start. Easy to source, cheap to purchase and will work for most cases.
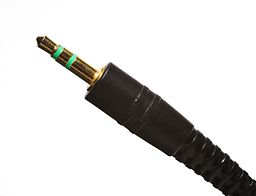
Likewise, for a small number of higher current conductors, the common PC power supply connectors are inexpensive and easily found at most parts distributors.
The type of signals most of our customers are working with are generally a good fit for the variety of DIN connectors: these are easy to find for between two to eight conductors and since they are popular in the professional audio field, are generally inexpensive. They also have the benefit of being very easy to use; just decide how many contacts you need, and go. No special tools or separate contact, housings, strain reliefs, etc. need to be purchased.
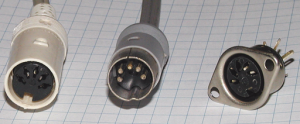
For maximum versatility, we like Circular connectors.
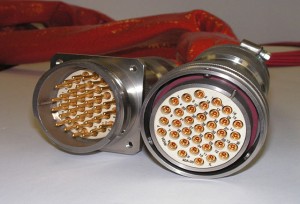
These are often referred to as “Cannon” connectors from the company who popularized them for industrial and military use. Their use spans the range from very low level millivolt signals, to high voltage, high current applications.
Circular Plastic Connectors are less expensive than the metal versions, but retain the versatility. They can be complex since you need to match the connector shell with the appropriate pin size, perhaps add a backshell, cable clamp or seal, and decide on crimp or solder type connectors. But if you need to securely connect a few dozen signals in a harsh environment, they are definitely worth a look.
If you’d like to subscribe to this blog, please click here.